Page Name
How to Receive Products into the Warehouse
Receiving products in a warehouse is a crucial step in the supply chain process. It ensures that products are accurately accounted for, organized, and stored efficiently for future distribution. Whether you are receiving a large shipment or smaller batches, knowing the right methods and workflows to manage this process can significantly impact your operational efficiency.
Methods to Receive Products
There are generally two main ways to receive products into a warehouse:
Blind Receipt and Receiving against PO/ASN.
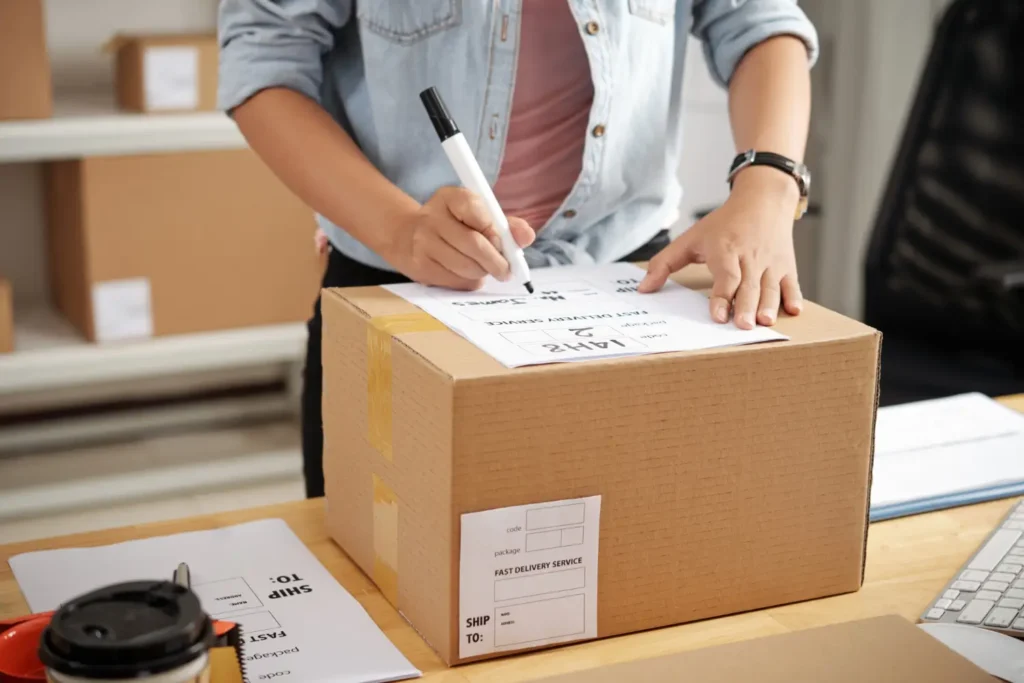
Blind Receipt
Blind receipt is a method where products are received without any accompanying packing lists or purchase orders. In this case, the warehouse personnel manually enter the details of each SKU (Stock Keeping Unit) and the respective quantities as they are checked in.
Manual SKU Entry: The staff will manually identify and log each item, which requires thorough attention to detail. This process can be slower compared to receiving with a packing list, but it ensures that each item is carefully accounted for.
Accuracy is Key: Since no external documentation is provided, this method requires precise counting and SKU matching to avoid inventory discrepancies.
Useful for Unscheduled Deliveries: Blind receipts may be employed when suppliers deliver products unexpectedly or when documentation is delayed.
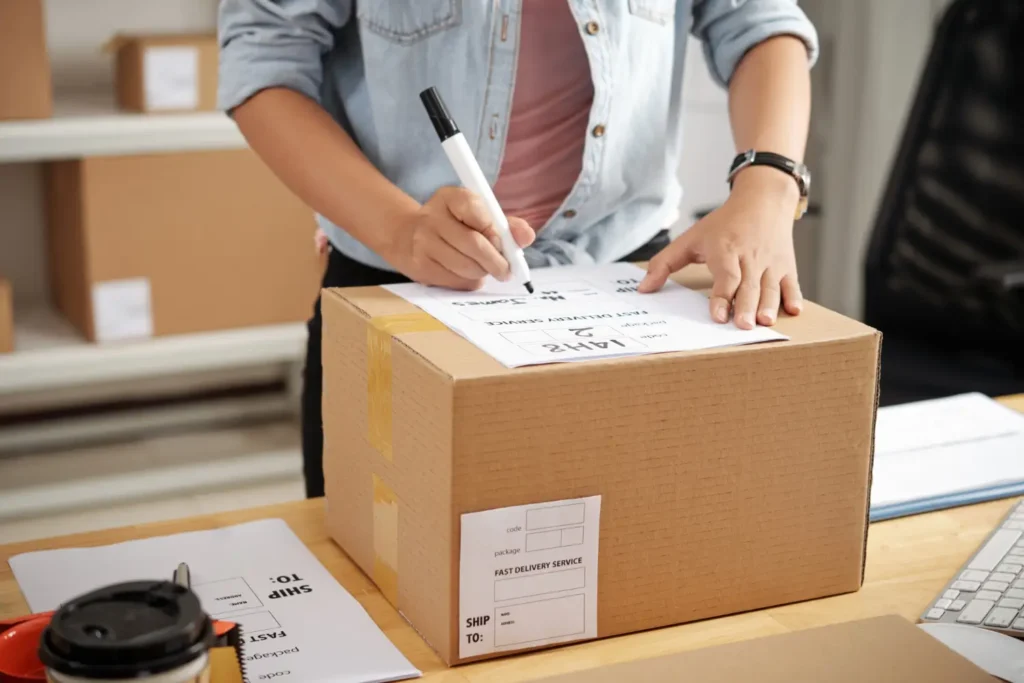
Receiving Against PO/ASN
Receiving against a PO (Purchase Order) or ASN (Advance Shipping Notice) is the more common method used in modern warehouses. This system ensures that the products received match a pre-existing order, which makes the process faster and more organized.
PO Created by Customer: Typically, your customer will log in to their designated portal and create the PO and packing list before shipping the products to your warehouse.
Vendor/ Supplier Involvement: There is also the flexibility for vendors or suppliers to directly log in to the same portal and create a packing list when they ship products. This ensures a smooth flow of information and minimizes confusion during receiving.
Efficient Matching Process: When the shipment arrives, the warehouse team compares the items in the delivery to the details on the PO or ASN, confirming the quantities and SKUs match.
Receiving Workflow Explained
To manage your warehouse effectively, it’s essential to have a streamlined process for receiving products. Whether you’re using Blind Receipt or Receiving against PO/ASN, the overall workflow remains similar:
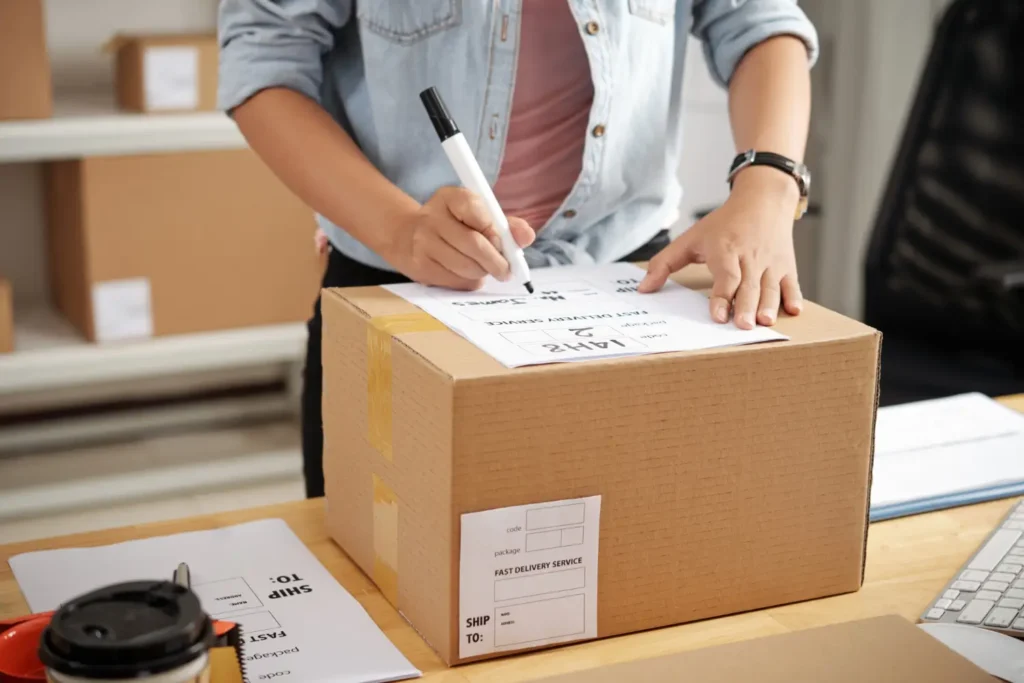
Step - 1
PO Creation
Your customer (or supplier) will create the Purchase Order (PO) or packing list in your system before shipping the products. This document will outline the items, SKUs, and quantities expected to be delivered.
Step - 2
Receipt of Products
-Upon arrival, the warehouse team begins the process of receiving the shipment. This involves unloading the products from the truck, trailer, or container.
– In the case of Blind Receipt, the team manually enters all the item information.
– For Receiving against PO/ASN, the staff cross-references the incoming items with the details on the PO or packing list.
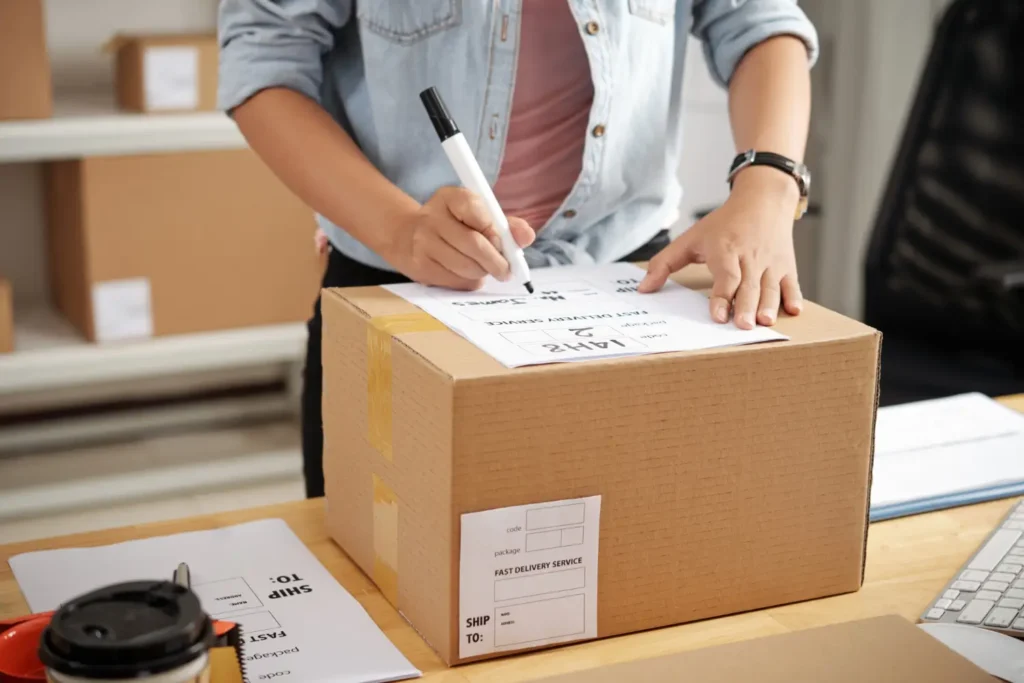
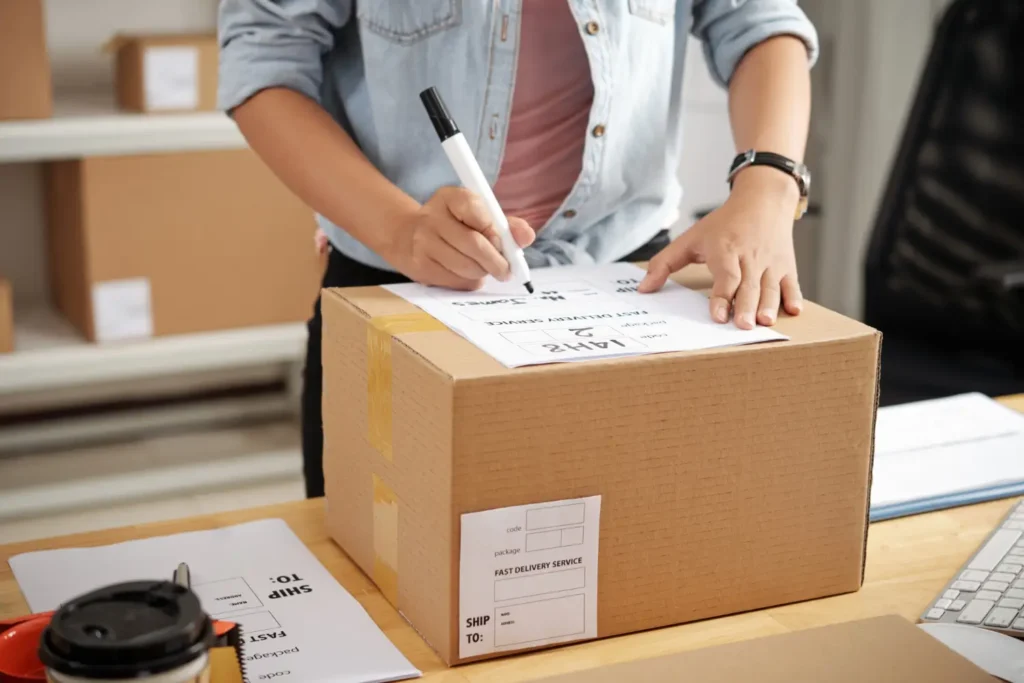
Step - 3
Supervisor Quality Control
– Once the items are received, the warehouse supervisor inspects the shipment to ensure everything is in order. Quality control checks for damages, missing items, or incorrect SKUs that may have been sent in error.
– Any discrepancies are documented at this stage to maintain clear communication with the customer or vendor.
Step - 4
Confirm Receipt
– After the quality check, the team confirms the receipt of the shipment. This involves verifying that all products have been accounted for and are free of any issues.
– The confirmation is logged into the warehouse management system, ensuring that the inventory is updated in real time.
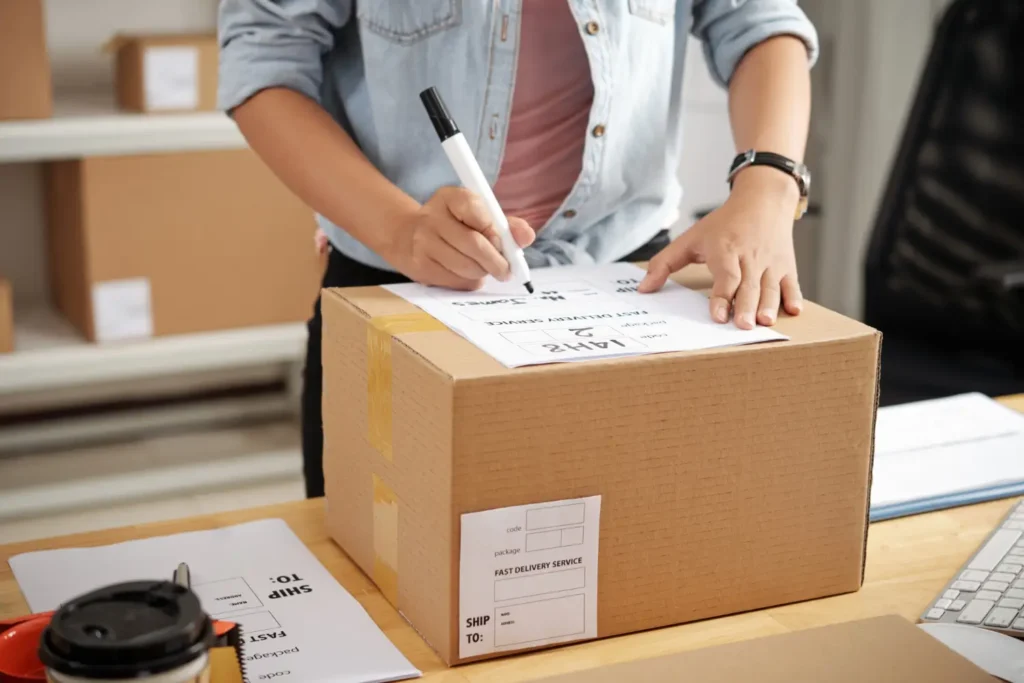
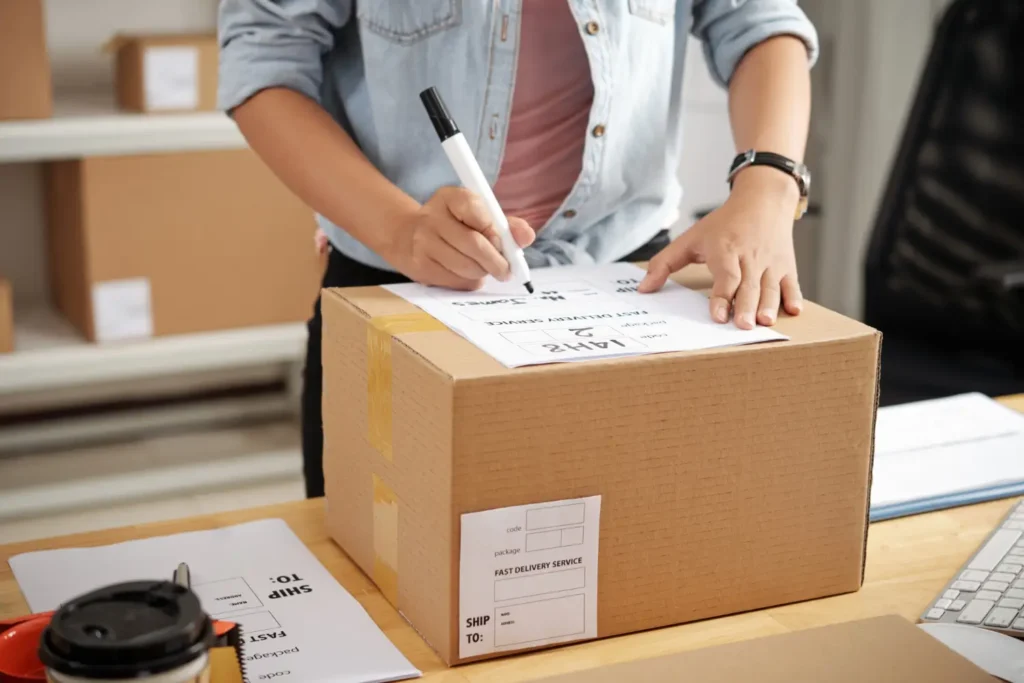
Step - 5
Put Away
– Once the receipt is confirmed, the Packem system automatically generates a “Put Away” task for the warehouse team.
– Using handheld scanner devices, warehouse workers are directed to the appropriate locations where each SKU will be stored.
– Products are then efficiently moved to their designated spots within the warehouse, making them available for future picking, packing, and shipping.
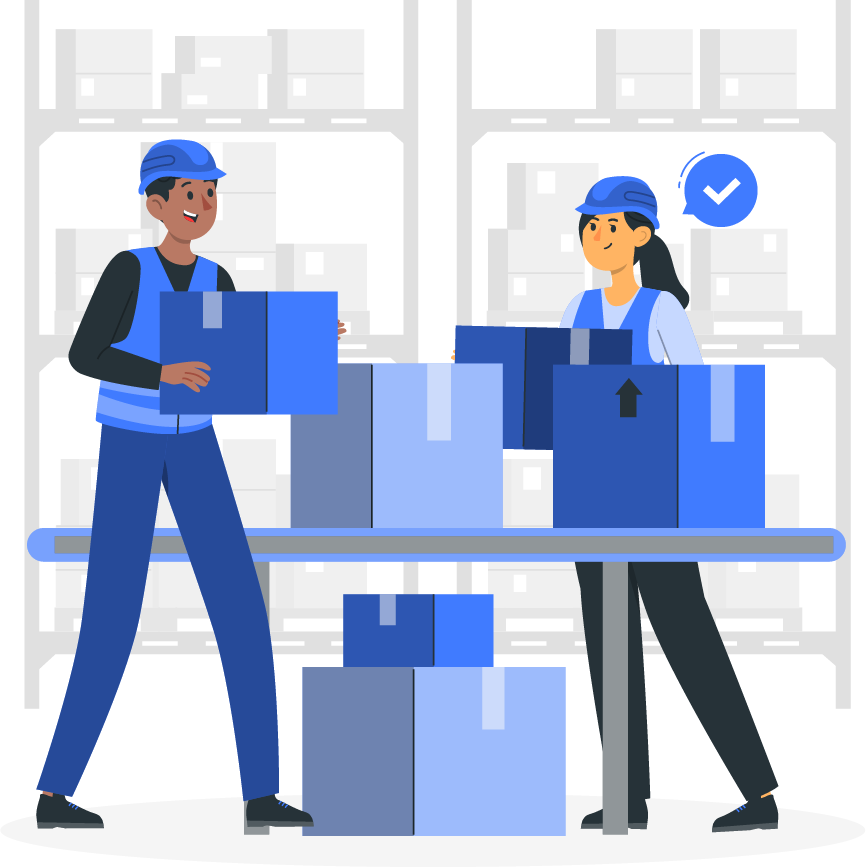
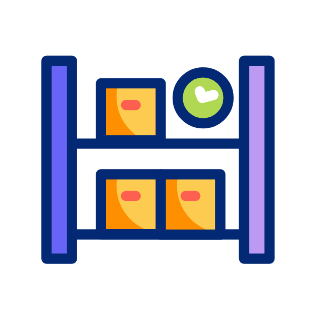
Tips for Efficient Product Receiving in Warehouses
- Train Your Team: Ensure all warehouse staff are well-trained in using handheld scanners and the Packem system to receive and put away products accurately.
- Monitor Quality Control: Always have a supervisor double-check the received goods to catch any issues early on.
- Optimize Your Space: Efficient put-away procedures rely on well-organized warehouse shelving and storage systems. Regularly review your layout to maximize space utilization.
- Keep Communication Open: Maintain strong communication with your suppliers, vendors, and customers to ensure clear expectations during the receiving process.
- Use Technology: Take advantage of warehouse management software (like Packem) to automate tasks and provide real-time inventory insights.
BENEFITS OF PACKEMWMS
Advantages of Using the Packem System for Product Receiving
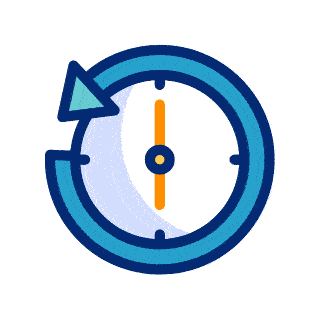
Real-Time Inventory Updates
The system automatically updates your inventory records as products are received and confirmed. This real-time tracking reduces the chance of errors and ensures that your stock levels are always accurate.
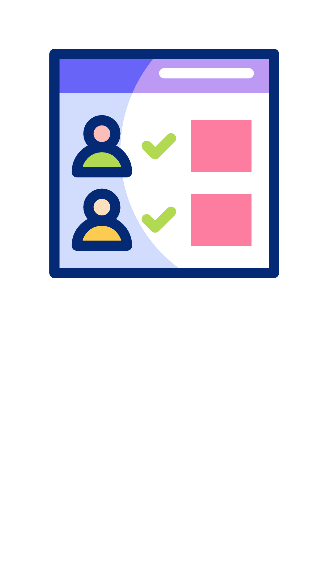
Automated Task Assignment
Packem generates a "Put Away" task immediately after the receipt is confirmed, allowing warehouse workers to focus on efficient organization. The tasks can be completed using handheld scanners, further optimizing the workflow.
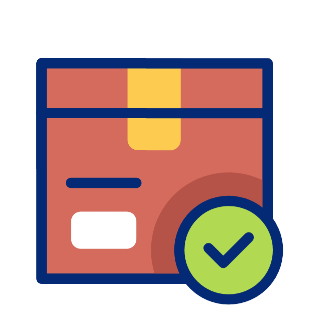
Improved Accuracy
Whether you are working with Blind Receipts or receiving against a PO/ASN, the Packem system enhances accuracy by matching SKUs and quantities during the receipt process. This minimizes discrepancies and keeps your inventory in check.
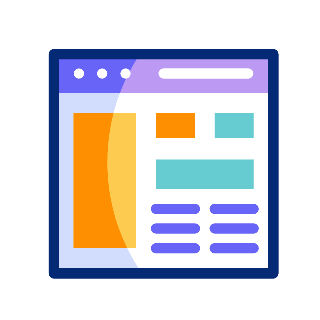
Seamless Vendor and Customer Integration
With the ability for vendors and customers to log into the portal and create POs or packing lists. This reduces errors in shipment documentation and creates a smooth receiving process.
DO YOU KNOW?
Frequently Asked Questions
Blind receipt is a method where warehouse staff receive products without any pre-provided packing list or purchase order. They manually enter SKUs and quantities during the receiving process.
In receiving against PO/ASN, the warehouse receives products based on a purchase order or advanced shipping notice created by the customer or supplier. The items in the shipment are matched against this order for accuracy.
A “Put Away” task is an instruction generated by the warehouse system after products are received and confirmed. It directs workers to store items in designated locations within the warehouse.
The Packem system automates the receiving process by generating tasks, updating inventory in real time, and allowing customers and vendors to create POs and packing lists directly in the portal.
Quality control ensures that all received products are in good condition, with the correct SKUs and quantities. It helps prevent inventory discrepancies and ensures customer satisfaction.