Businesses are constantly seeking innovative strategies to enhance operational efficiency and reduce costs. One such strategy that has gained significant traction in recent years is warehouse cross docking.
By leveraging the example of CWI Logistics’ cross docking practices, we will delve into the world of warehousing, exploring its benefits, challenges, and best practices.
What Is Cross Docking?
Cross docking is a logistics practice that involves transferring goods from an inbound vehicle, such as a truck or a container, directly to an outbound vehicle for immediate delivery, with minimal or no storage time in between.
Unlike traditional warehousing models, where goods are received, stored, and then picked for orders, it eliminates the need for long-term storage, expediting the flow of products through the supply chain.
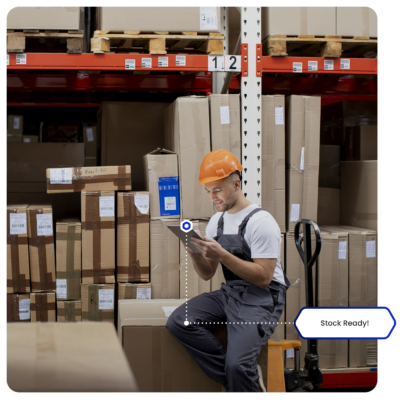
Benefits of Cross Docking
- Reduced Inventory Holding Costs: By minimizing or eliminating the need for storage, cross docking reduces inventory holding costs associated with warehousing, including rental space, labor, insurance, and security.
- Increased Operational Efficiency: Cross docking allows for the streamlined movement of goods, eliminating unnecessary handling and reducing the time required to process orders. This leads to faster order fulfillment and improved customer satisfaction.
- Cost Savings: By optimizing the supply chain and reducing handling and storage requirements, it can significantly lower transportation costs, as fewer vehicles and miles are required to move goods from the manufacturer to the end customer.
- Enhanced Agility: Enables businesses to respond quickly to changing market demands and customer expectations. It facilitates just-in-time inventory management and enables rapid order fulfillment, supporting efficient supply chain operations.
Experience the simplest inventory management software.
Are you ready to transform how your business does inventory?
Challenges Of Cross Docking
While cross-docking offers numerous benefits, implementing and managing a successful operation comes with its own set of challenges. Here are some common obstacles that businesses may encounter:
- Supply Chain Coordination: Effective cross-docking relies on close collaboration and coordination among suppliers, carriers, and distribution centers. Establishing strong relationships and implementing robust communication channels are essential to ensure the smooth flow of goods.
- Inventory Visibility and Accuracy: Maintaining accurate real-time inventory data is crucial for your success. Advanced tracking technologies, such as RFID tags and barcode scanners, can help ensure accurate product identification and efficient inventory management.
- Complex IT Infrastructure: A reliable and integrated information technology (IT) infrastructure is essential for managing effective operations. Investing in a robust warehouse management system (WMS) that can handle the complexities of cross docking can streamline operations. The software development agency at Mozym specializes in warehousing and logistics software.
Best Practices
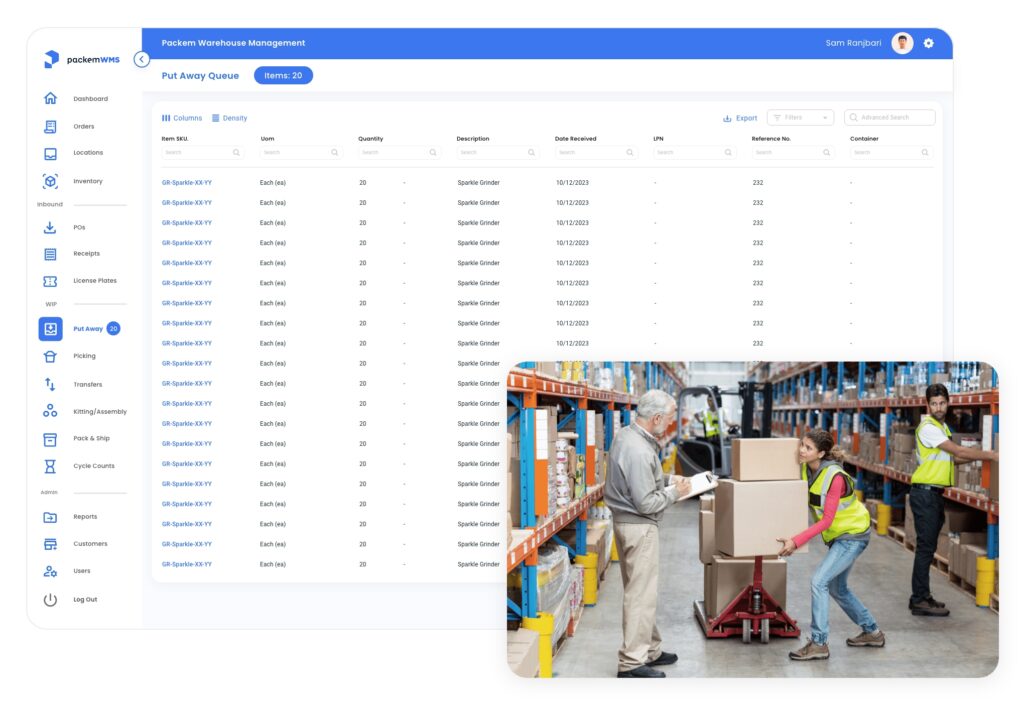
Here are some tips for effectively implementing cross-docking in the warehousing and 3PL (Third-Party Logistics) industry:
- Continuous Improvement: Regularly reviewing and analyzing operations, collecting data, and implementing process improvements based on performance metrics can help drive ongoing efficiency gains and maintain a competitive edge.
- Thorough Planning and Analysis: Before implementing cross-docking, analyze your supply chain to ensure it is suitable for this process. Understand your product types, volumes, and the predictability of your supply and demand.
- Invest in Technology: Utilize a robust warehouse management system (WMS) that supports cross-docking. Technology can help track inventory in real-time, manage orders efficiently, and ensure accurate, timely movement of goods.
- Efficient Warehouse Layout Design: Design your warehouse to facilitate cross-docking. This might include having specific docks designated for incoming and outgoing shipments, and minimal distance between these points to reduce handling time.
- Time Coordination: Coordinate the arrival of incoming goods with outgoing transportation. This synchronization is crucial to minimize the time goods spend in the warehouse.
- Quality Control: Implement stringent quality control measures. Since products are not stored, identifying defects or errors at the docking stage is essential to prevent returns and customer dissatisfaction.
- Staff Training and Management: Ensure your staff is well-trained in cross-docking procedures. Efficient and knowledgeable handling of goods is crucial for the success of cross-docking operations.
- Partner Communication and Collaboration: Maintain excellent communication with suppliers and customers. Forecasting, advanced shipping notifications, and real-time communication help in aligning supply with demand.
- Flexible and Scalable Operations: Be prepared to scale operations up or down based on demand fluctuations. Flexibility in handling different types of products and order sizes is also important.
- Regular Performance Monitoring: Continuously monitor the performance of your cross-docking operations. Key performance indicators (KPIs) might include the time taken for cross-docking, accuracy of shipments, and costs saved.
- Continuous Improvement: Be open to adapting and improving your cross-docking processes. Regularly review procedures, incorporate feedback, and stay informed about new technologies or methods.
- Emergency Preparedness: Have a contingency plan for unexpected issues, such as delayed shipments or damaged goods. This ensures minimal disruption to the supply chain.
In Conclusion
PackemWMS is designed with the end-user in mind. Its intuitive interface ensures that your team can quickly adapt to the new system, minimizing downtime and training costs. The user-friendly design makes it an ideal choice for warehouses looking to transition to modern technology without the headache of a steep learning curve.