Page Name
Inventory and Kitting: Streamlining Your Warehouse Operations
Effective inventory management and kitting are essential elements of running a smooth warehouse operation. Managing inventory efficiently ensures that products are always available when needed, while kitting simplifies the assembly and packaging process. Whether you’re creating kits to order or stocking pre-assembled kits, having the right system in place to manage inventory, generate bills of material, and track work orders is crucial.
With Packem’s advanced features, you can create kits, manage bills of materials (BOM), generate work orders for kitting jobs, and streamline your inventory management with powerful filters and advanced search functions. This guide will walk you through the fundamentals of inventory and kitting, how these processes work, and how Packem’s tools can help optimize your warehouse operations.
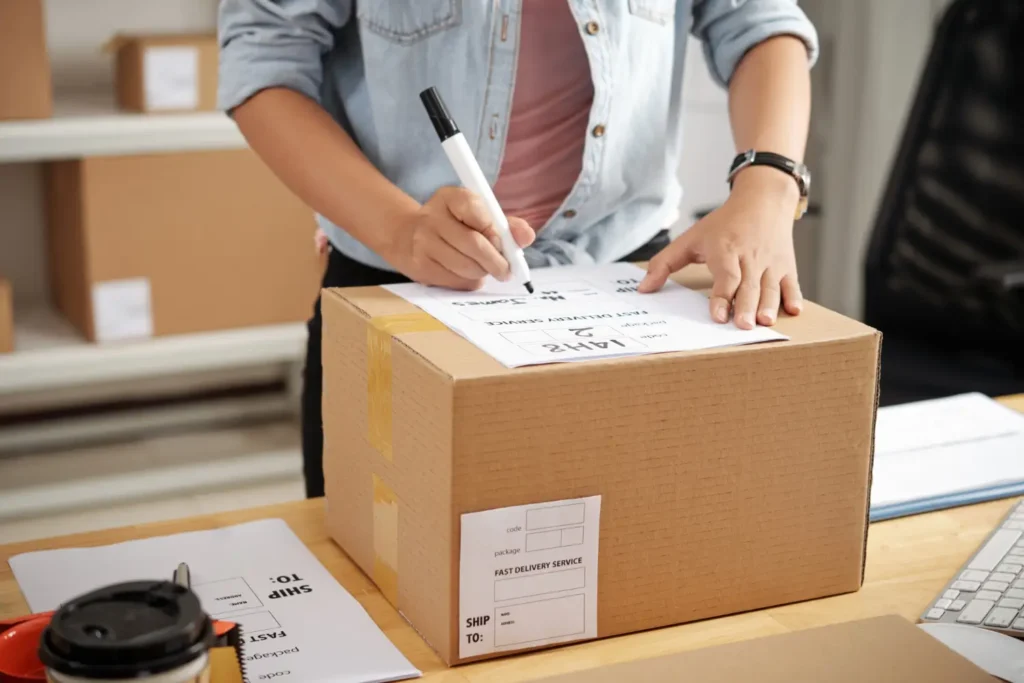
What is Inventory Management?
Inventory management involves tracking, controlling, and optimizing stock levels in your warehouse. It ensures that you have the right amount of product on hand to meet customer demand while minimizing excess stock that takes up space and ties up capital.
- Inventory Tracking: Monitoring stock levels in real-time across various warehouse locations.
- Stock Replenishment: Ordering new stock when levels fall below a set threshold.
- Forecasting Demand: Using historical data to predict future inventory needs and prevent stockouts or overstocking.
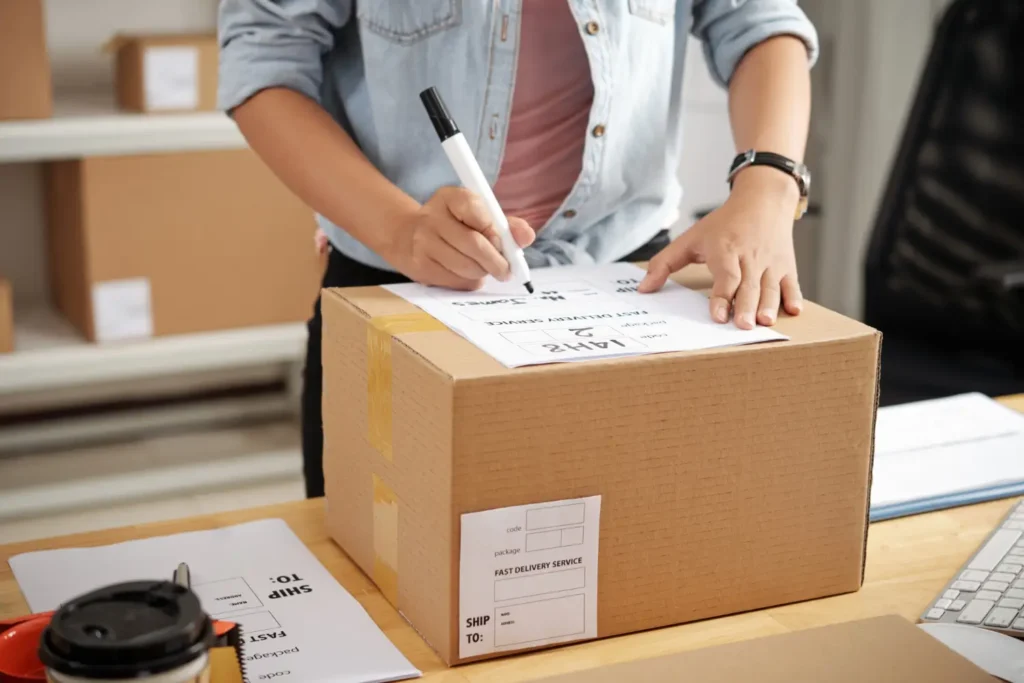
What is Kitting?
Kitting is the process of grouping multiple individual items or components together into a single package, often referred to as a “kit.” Kitting can be done either to order (assembling kits when a customer places an order) or to stock (assembling kits in advance and storing them for future orders).
- Kit to Order: The components are picked and assembled when an order is placed, ensuring that the kit is customized for each customer.
- Kit to Stock: Pre-assembled kits are stocked in the warehouse, ready to be picked and shipped as soon as an order comes in.
Kitting improves efficiency, reduces errors, and enhances customer satisfaction by providing bundled products that are ready for use.
How Kitting Works: A Step-by-Step Process
Kitting involves several steps, from defining the components of a kit to creating the necessary work orders and assembling the kit itself. Below is an outline of how the kitting process works:
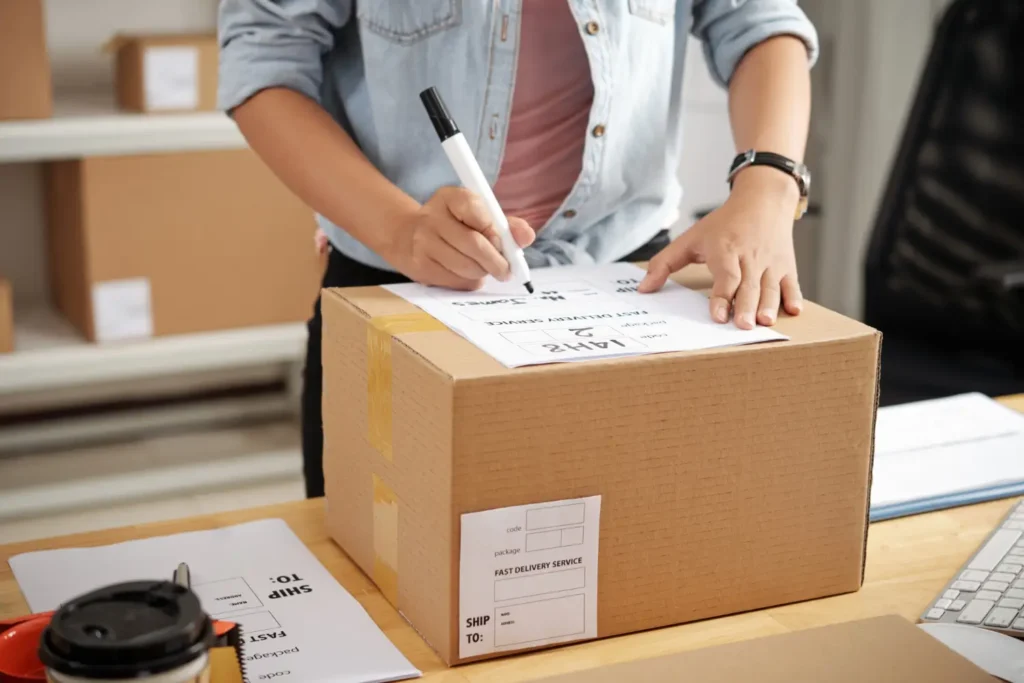
Step - 1
Create a Kit
The first step in kitting is defining what goes into the kit. Each kit is composed of individual items or SKUs, and these need to be grouped together in your inventory system.
- Define Components: Choose the products or components that will make up the kit. For example, if you’re creating a “computer setup” kit, it might include a monitor, keyboard, mouse, and cables.
- Assign SKUs to the Kit: Each kit receives its own SKU in the inventory management system, making it easy to track and manage.
Step - 2
Bill of Materials (BOM)
A Bill of Materials (BOM) is a comprehensive list of all the parts and components required to assemble a kit. It includes the quantities of each item, helping to ensure you have enough stock on hand to complete the kits.
- List of Components: The BOM lists every item needed for the kit, including quantities.
- Inventory Check: The system checks whether all components are available in the required quantities before starting the kitting process.
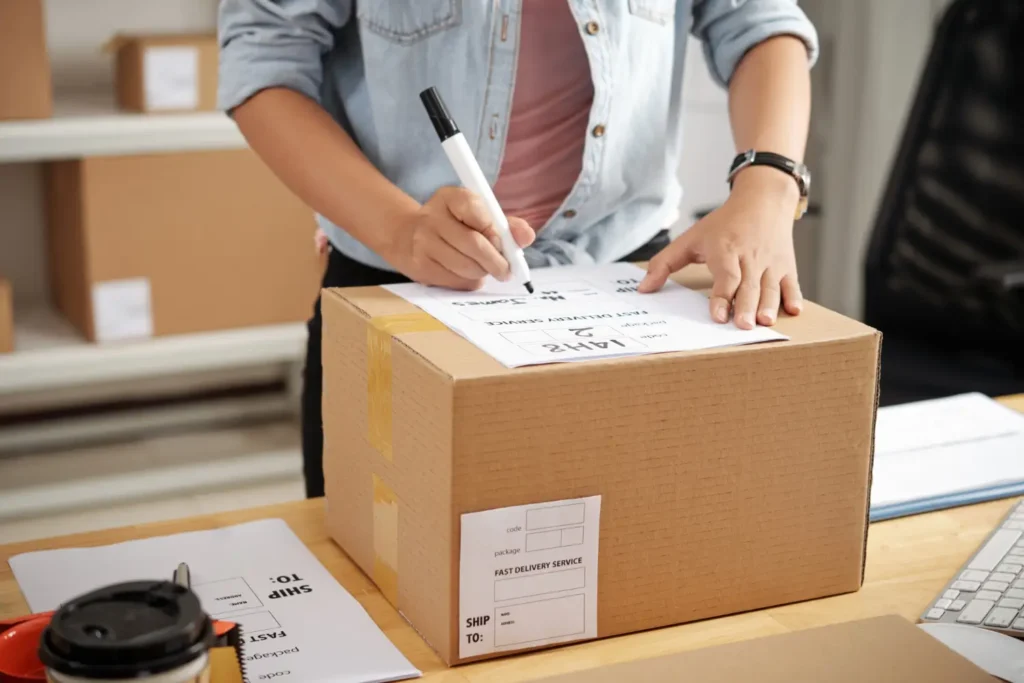
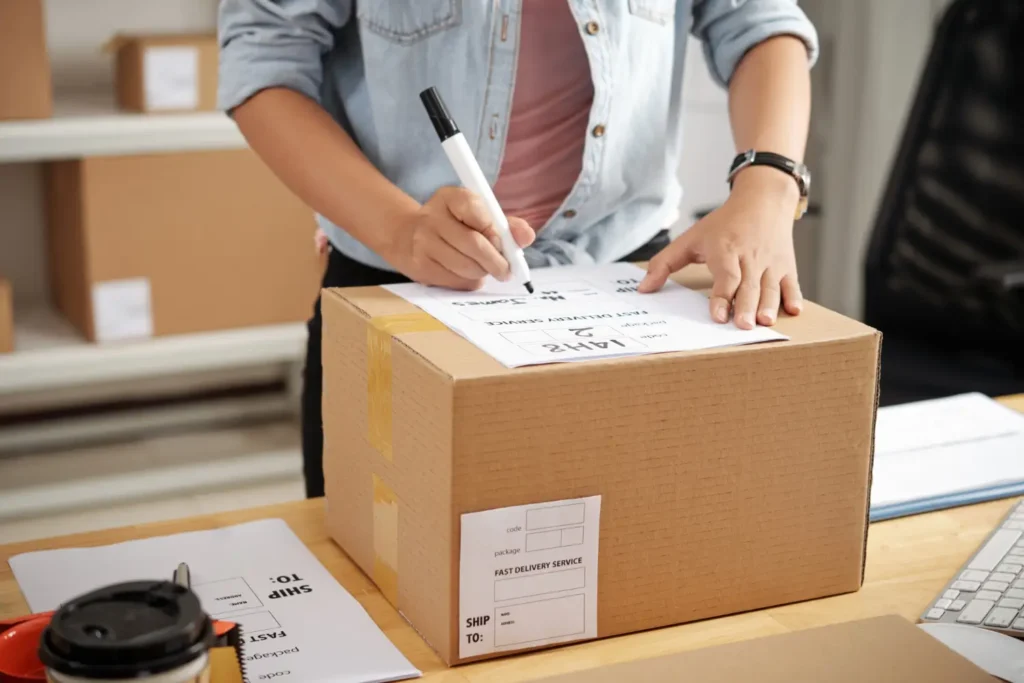
Step - 3
Generate Work Orders for Kitting Jobs
Once the components and BOM are defined, the next step is to generate work orders for kitting jobs. A work order outlines the specific tasks needed to assemble a kit, assigning responsibilities and tracking progress.
- Assign Tasks: The system generates work orders that detail who will be responsible for assembling the kits, the quantity to be built, and the required completion date.
- Track Progress: Work orders help you monitor the status of kitting jobs, ensuring that kits are assembled on time and to the correct specifications.
Step - 4
Assemble the Kit
With the work order in hand, warehouse workers assemble the kit by gathering the components, packaging them together, and preparing them for storage or shipment.
- Pick Components: Workers pick the individual components from inventory based on the BOM.
- Assemble the Kit: The components are grouped together, packaged, and labeled with the kit’s SKU.
- Update Inventory: Once the kit is assembled, the system updates the inventory to reflect the decrease in individual components and the addition of completed kits.
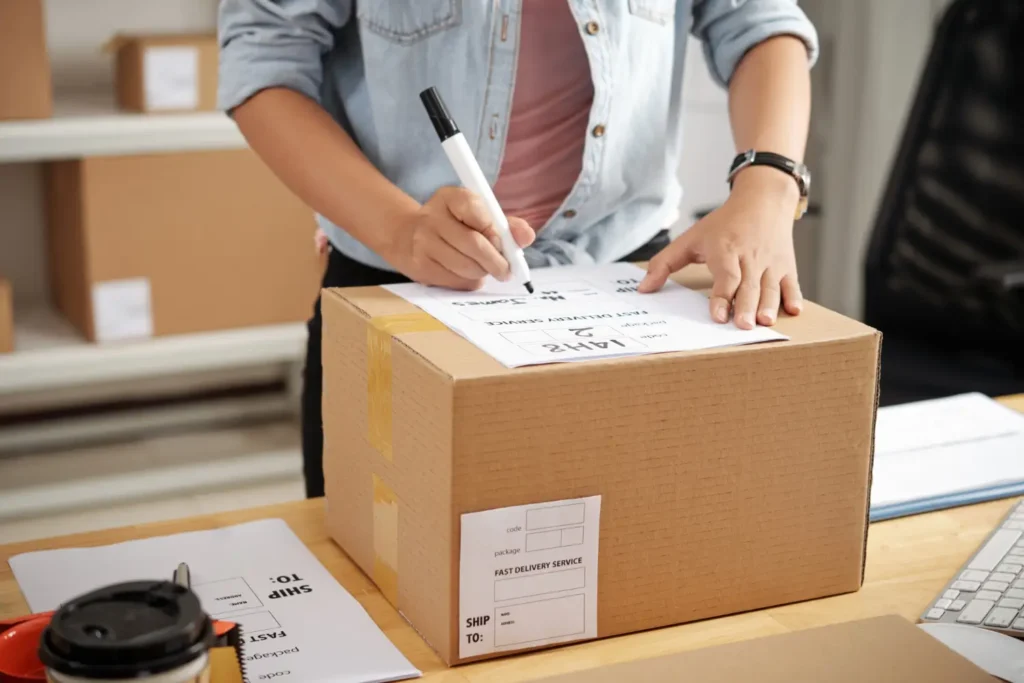
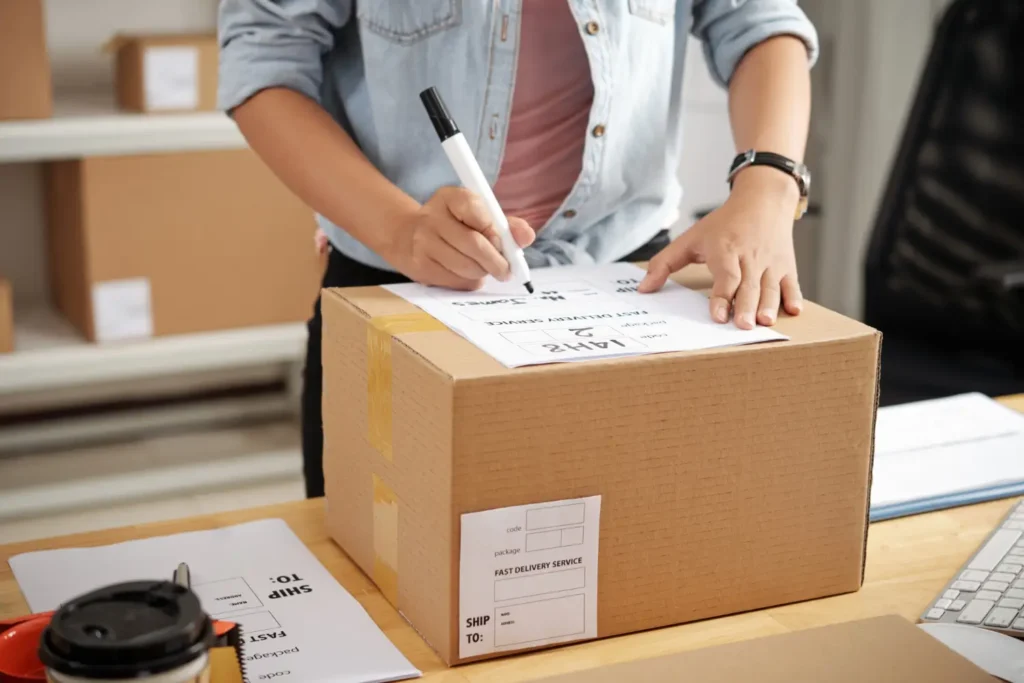
Step - 5
Kit Storage or Shipment
Depending on whether you’re kitting to order or kitting to stock, the finished kit is either stored in the warehouse for future orders or immediately prepared for shipment.
- Kit to Stock: The assembled kits are stored in the warehouse, ready to be picked and shipped when orders come in.
- Kit to Order: The kit is shipped directly to the customer as soon as it’s assembled.
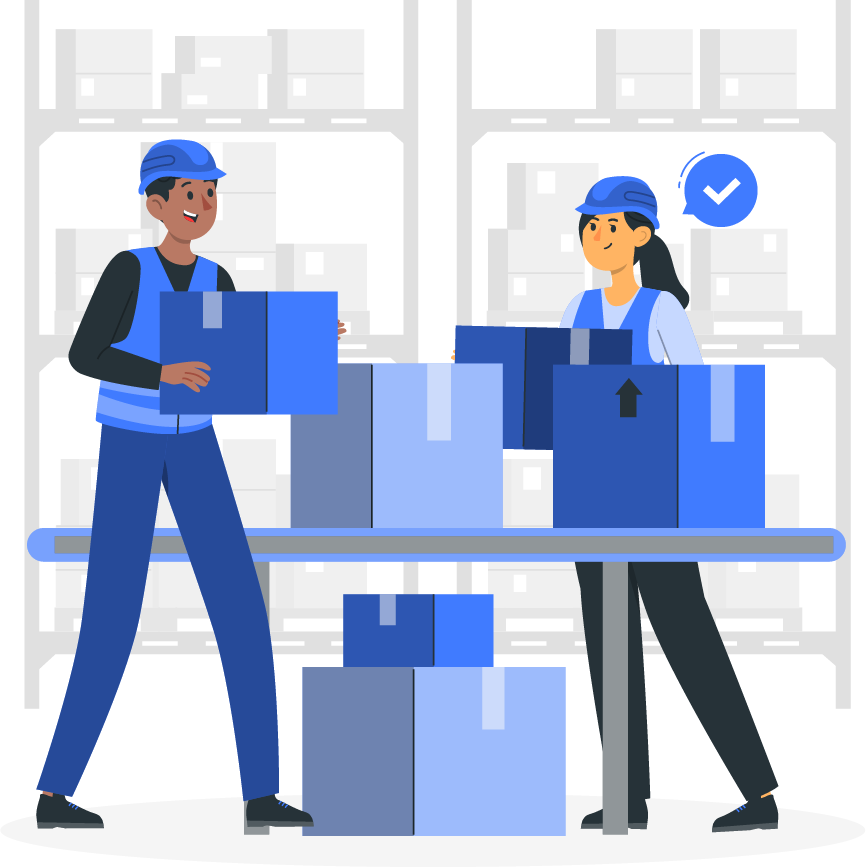
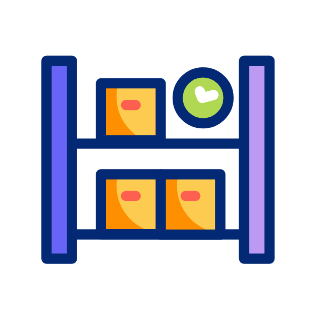
How Packem Improves Kitting and Inventory Operations
- Simplify Kit Creation: Creating kits with Packem is a breeze. The system allows you to define the components of each kit, assign SKUs, and generate BOMs in just a few clicks.
- Efficient Work Order Management: Packem’s work order system ensures that kitting jobs are completed on time and according to specifications. With clear task assignments and progress tracking, you can manage multiple kitting jobs simultaneously with ease.
- Advanced Inventory Control: With Packem’s advanced inventory management features, you can keep track of every SKU, component, and kit in your warehouse. The system provides real-time updates on stock levels, making it easy to manage reordering and avoid stockouts.
Best Practices for Effective Inventory and Kitting Management
To ensure your warehouse runs efficiently, consider the following best practices for managing inventory and kitting
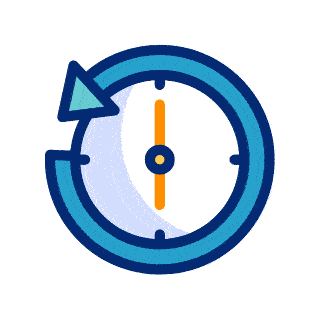
Organize Your Inventory
Keep your warehouse organized by grouping similar items together and clearly labeling all SKUs. This will make it easier to locate components during the kitting process and reduce picking errors.
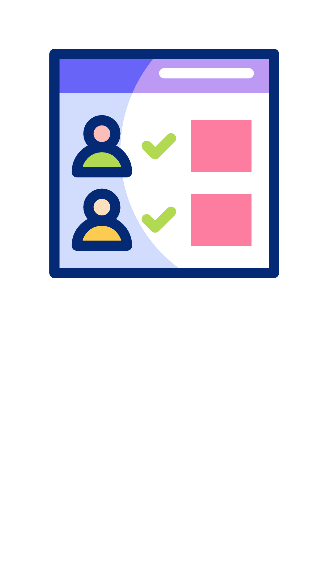
Monitor Stock Levels
Regularly check your inventory levels to ensure you have enough stock on hand to complete kitting jobs. Use Packem’s real-time inventory tracking and automated alerts to stay on top of stock levels.
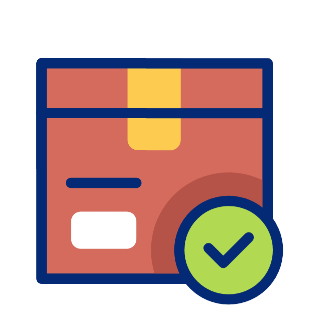
Use Barcode Scanning Technology
Implement barcode scanning technology to speed up picking, kitting, and inventory tracking processes. Scanning reduces human error and ensures accurate inventory management.
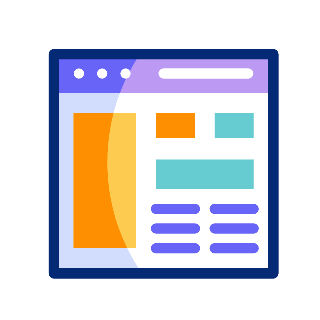
Automate Reordering
Set up automated reordering systems based on stock level thresholds to prevent stockouts. This ensures that you always have the necessary components for kitting jobs on hand.
DO YOU KNOW?
Frequently Asked Questions
Kitting is the process of assembling multiple individual components into a single package or kit, which can then be stored or shipped to customers. Kits can be created to stock or to order, depending on operational needs.
A Bill of Materials (BOM) is a detailed list of all the parts, components, and materials needed to assemble a product or kit. It ensures that all necessary items are available before starting the assembly process.
Packem simplifies the kitting process by allowing you to create kits, generate BOMs, and manage work orders. The system tracks inventory levels, ensuring that you have the necessary components on hand to complete kitting jobs.
Kit to stock refers to pre-assembling kits and storing them in the warehouse for future orders. Kit to order involves assembling the kit after a customer places an order, allowing for more customization.
To improve inventory management, use real-time tracking, automated stock alerts, and demand forecasting. Organize your inventory, implement barcode scanning, and use an efficient warehouse management system like Packem to optimize your operations.