Page Name
PO and Reorder Management: Streamlining Stock Control with Smart Reordering
Effective Purchase Order (PO) and Reorder Management is critical for maintaining optimal inventory levels in your warehouse. Ordering too much or too little can disrupt your supply chain, leading to either excess stock or costly stockouts. That’s where Packem’s Smart Reordering feature steps in, making inventory management easier and more predictive. This feature not only helps you keep track of your stock levels at different locations, but it also alerts you and your clients when it’s time to reorder from suppliers—automatically calculating reorder points based on key factors like lead time, safety stock, and sales velocity.
This guide will cover how PO and Reorder Management works, the importance of setting reorder points, and how Packem’s Smart Reordering can help you stay ahead of inventory needs without manual effort.
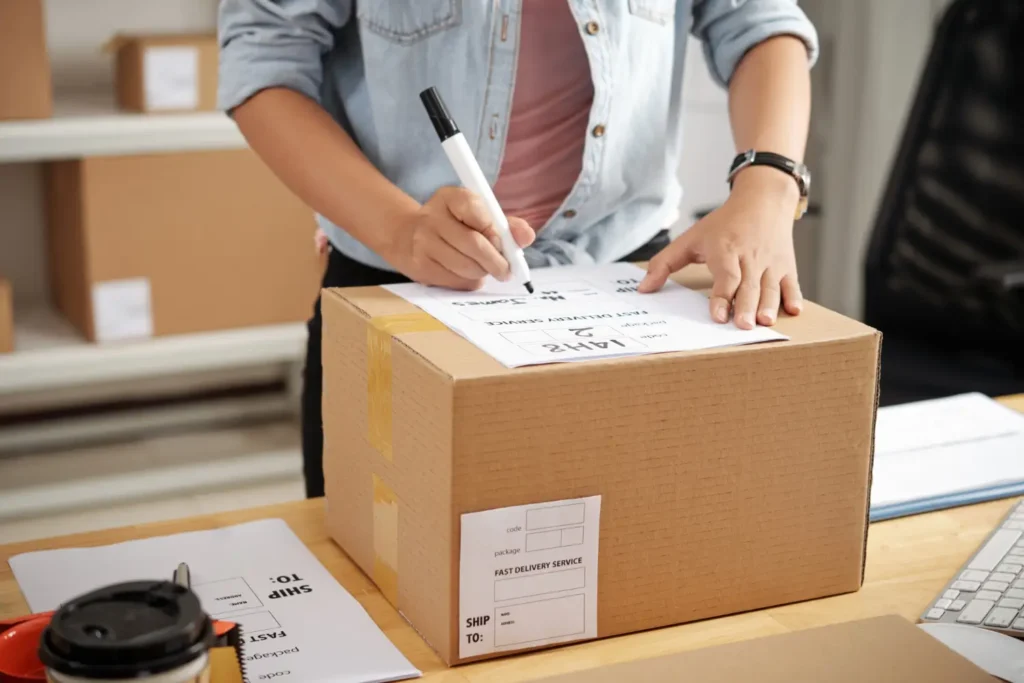
What is PO and Reorder Management?
PO (Purchase Order) Management is the process of overseeing the purchasing of stock from suppliers. It involves tracking purchase orders from the moment they are created, through approval and dispatch, until the goods are received in the warehouse. Reorder Management, on the other hand, ensures that stock levels are maintained by automating the reordering process before stockouts occur.
The goal of PO and reorder management is to ensure that the right products are available in the right quantities at the right time. By automating this process, you reduce the risk of human error, improve efficiency, and save time for more strategic tasks.
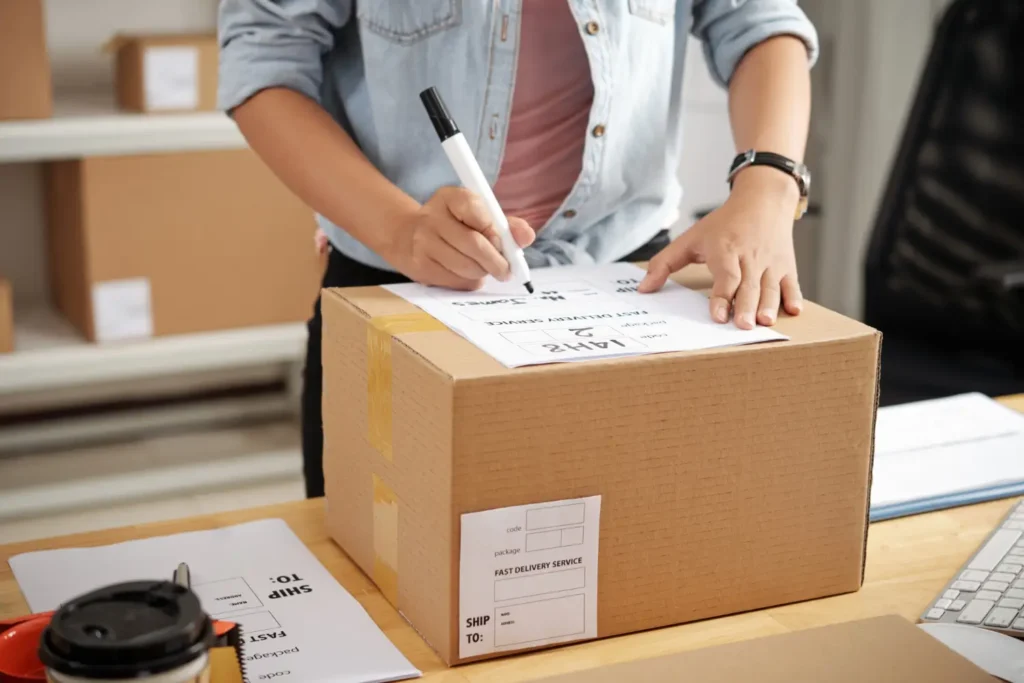
Key Components of Reorder Management
Lead time is the amount of time it takes from placing an order with your supplier to receiving the products in your warehouse. Understanding lead times is crucial because it affects how early you need to reorder products to avoid running out of stock.
Safety stock is a buffer of extra inventory that protects against unexpected demand spikes or delays in the supply chain. By maintaining safety stock, you can minimize the risk of stockouts.
Sales velocity refers to how quickly a product is selling over a given time period. Understanding your sales velocity helps you predict future demand and determine how much stock you’ll need.
The reorder point is the stock level at which you need to place a new order to avoid running out of stock. This is calculated based on your lead time, sales velocity, and safety stock.
How Smart Reordering Works in Packem
Packem’s Smart Reordering feature is designed to take the guesswork out of inventory management. By analyzing historical data, setting reorder points, and predicting future demand, Packem automatically alerts you and your clients when it’s time to reorder from suppliers. Here’s how the Smart Reordering system works:
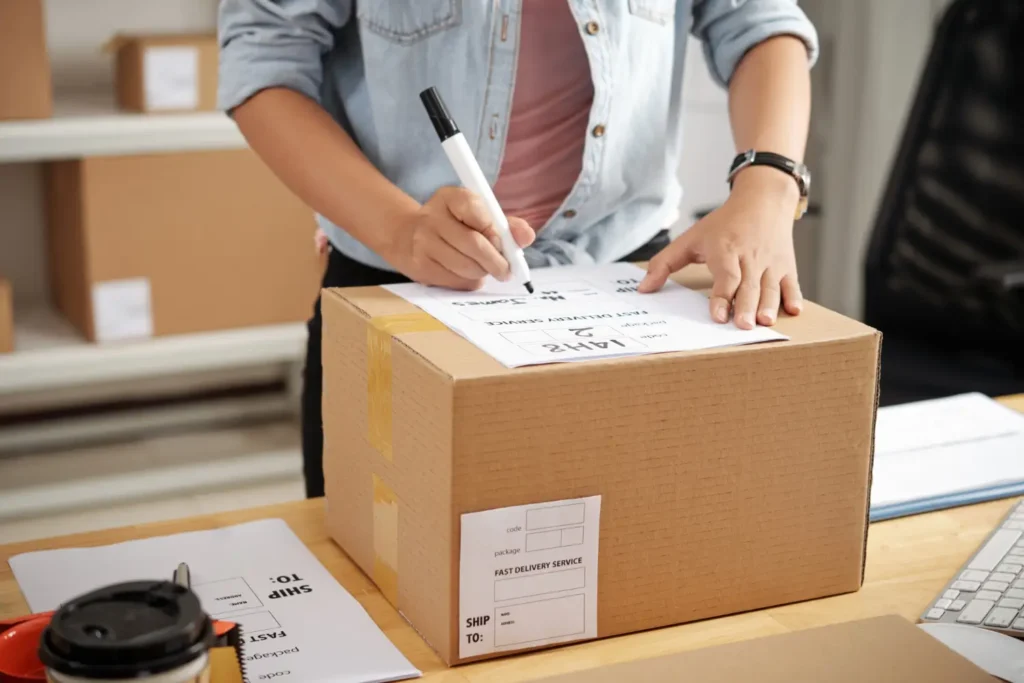
Step - 1
Predict Future Stock Needs
Packem’s system analyzes your inventory data to predict future product needs based on sales velocity, lead times, and safety stock. This predictive analysis helps ensure you always have the right amount of stock on hand without overordering.
- Sales Trend Analysis: The system uses historical sales data to identify patterns and predict future demand.
- Forecasting for Accuracy: With accurate forecasting, you can anticipate your stock needs and avoid last-minute reordering.
Step - 2
Automatic Reorder Alerts
Once the system determines that a product is approaching its reorder point, it sends automatic email alerts to both you and your client, prompting you to place a new order. This ensures that you never miss a critical reorder, helping you maintain consistent stock levels.
- Customizable Alerts: Alerts are sent when stock hits a predefined reorder point, ensuring timely action.
- Avoid Human Error: Automation reduces the risk of forgetting to reorder or miscalculating stock needs.
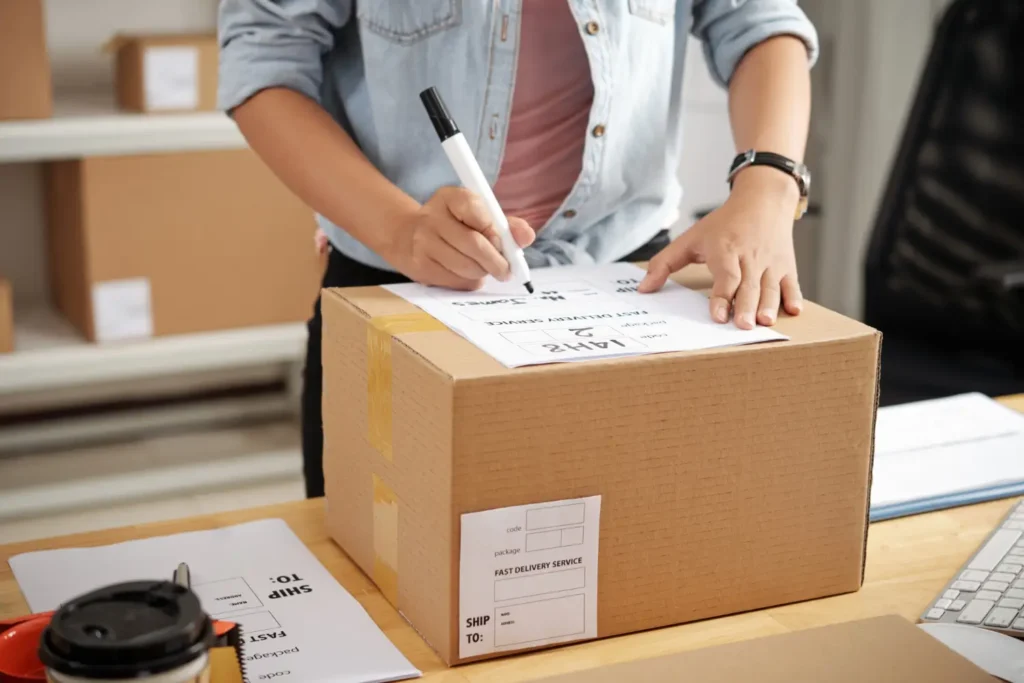
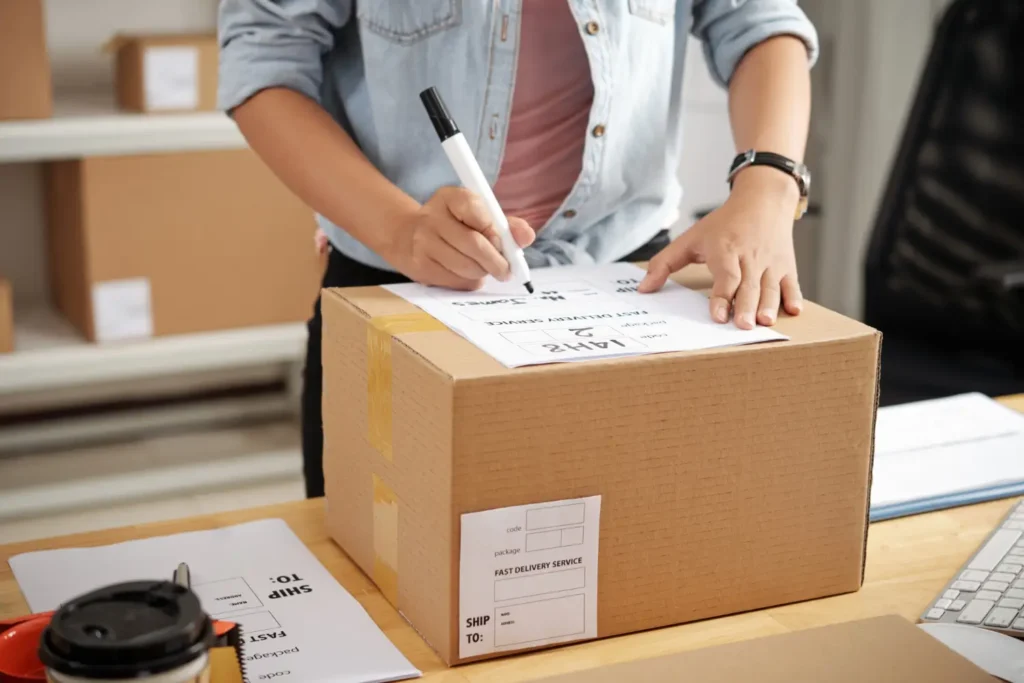
Step - 3
Multi-Location Stock Visibility
If you operate multiple warehouse locations, Packem’s Smart Reordering feature helps you keep track of stock levels across all locations. This gives you a clear picture of inventory availability, helping you make more informed reorder decisions.
- Stock Monitoring Across Locations: Get real-time insights into how much stock is available at each warehouse.
- Centralized Management: Manage reordering for multiple locations from a single platform, making it easier to oversee a large inventory network.
Step - 4
Setting Reorder Points
To use Smart Reordering effectively, you’ll need to set lead times, safety stock levels, and sales velocity for each product. Once these values are set, Packem will automatically calculate the reorder point and notify you when it’s time to reorder.
- Customizable Settings: Tailor lead times and safety stock levels for each product based on supplier performance and demand variability.
- Automated Calculations: Packem automatically calculates reorder points, taking the guesswork out of inventory management.
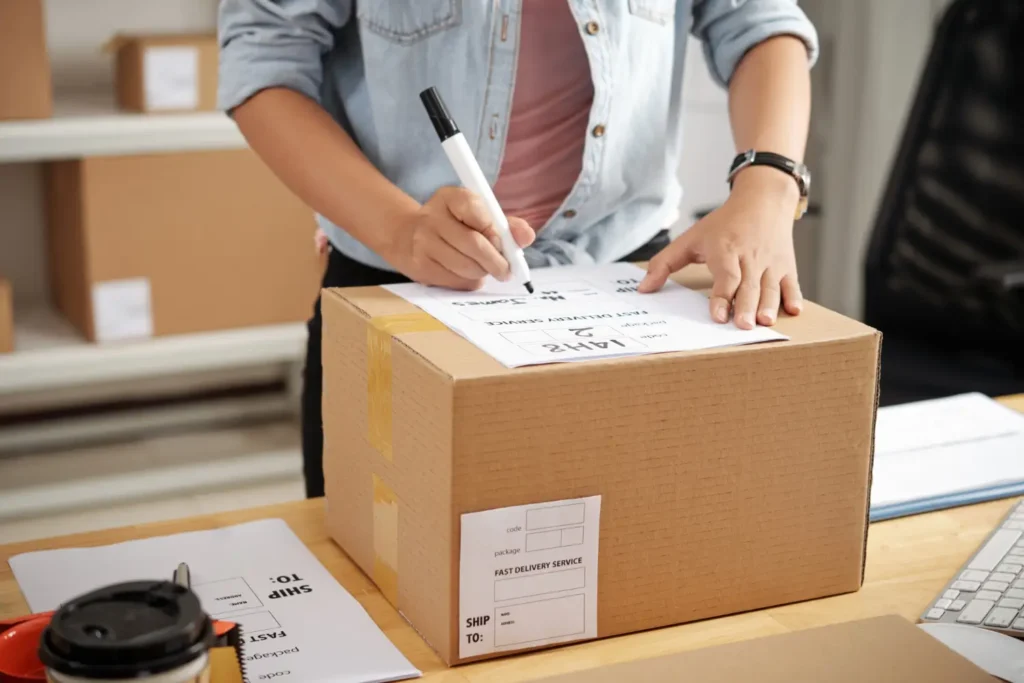
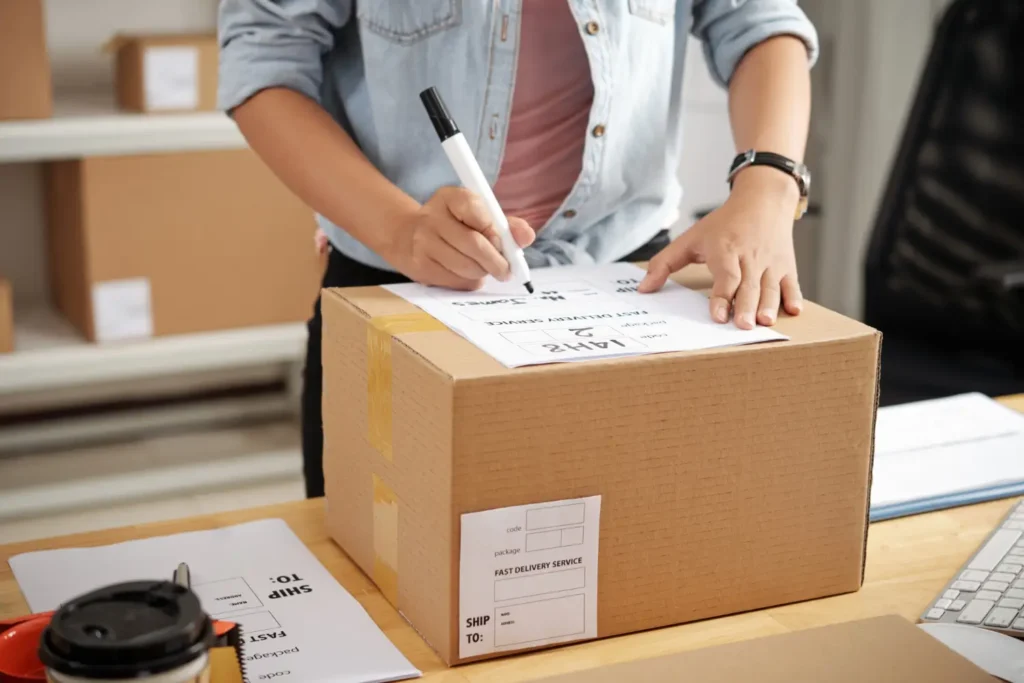
Step - 5
PO Creation
When stock levels hit the reorder point, Packem makes it easy to create and manage purchase orders directly within the system. You can generate POs, send them to suppliers, and track their status from creation to delivery.
- One-Click PO Generation: Automatically generate POs based on the system’s reorder recommendations.
- Supplier Tracking: Keep track of all your POs, from when they’re placed to when the goods are received in the warehouse.
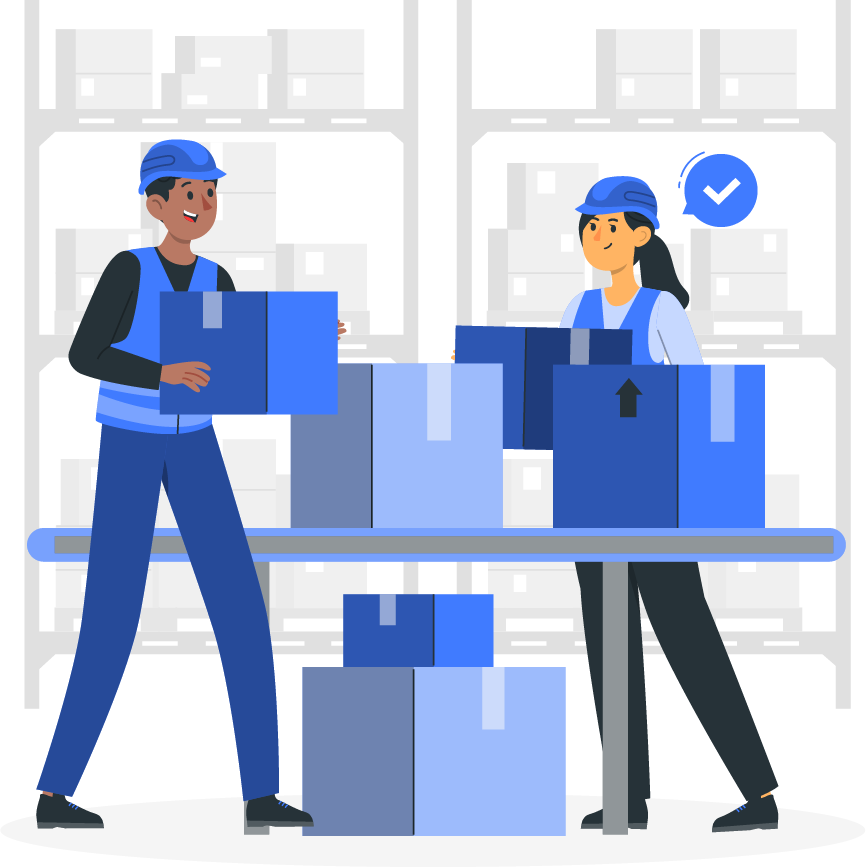
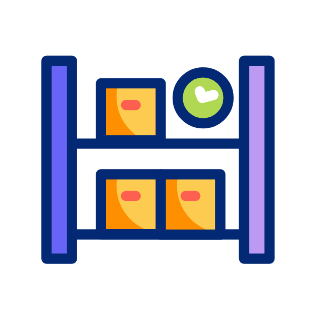
Benefits of Using Packem’s Smart Reordering for PO and Reorder Management
- Eliminate Stockouts: One of the biggest challenges in inventory management is avoiding stockouts, which can lead to lost sales and unhappy customers.
- Reduce Excess Inventory: Overordering can lead to excess stock, which takes up valuable warehouse space and ties up capital.
- Streamlined Purchase Order Management: Packem’s Smart Reordering integrates seamlessly with your PO management system, allowing you to generate, track, and manage purchase orders with ease.timely deliveries.
- Multi-Warehouse Management: For businesses with multiple warehouse locations, keeping track of inventory across different sites can be challenging.
- Improved Efficiency and Accuracy: By automating the reorder process, Smart Reordering reduces the risk of human error and ensures that stock levels are maintained accurately.
Best Practices for Effective PO and Reorder Management
To get the most out of your PO and Reorder Management processes, consider implementing these best practices
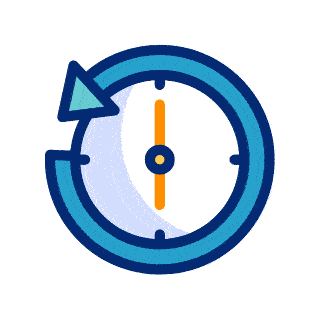
Set Accurate Lead Times
Make sure to set realistic lead times for each supplier based on past performance. This will ensure that reorder points are calculated accurately, preventing stockouts and delayed deliveries.
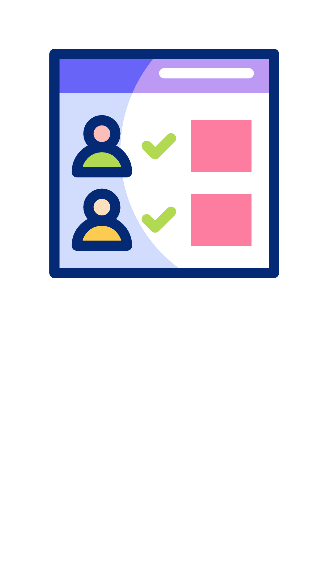
Regularly Review Sales Data
Keep an eye on your sales velocity and adjust reorder points as needed. Regularly reviewing sales data will help you stay on top of changing demand patterns and ensure that your stock levels are optimized.
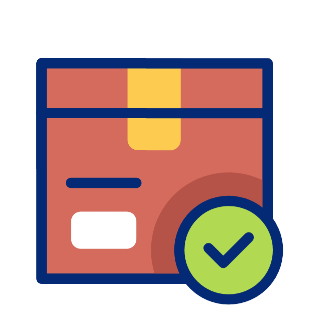
Maintain Adequate Safety Stock
Ensure that you always have enough safety stock to cover unexpected demand surges or supplier delays. Packem can help you calculate the right amount of safety stock based on historical data.
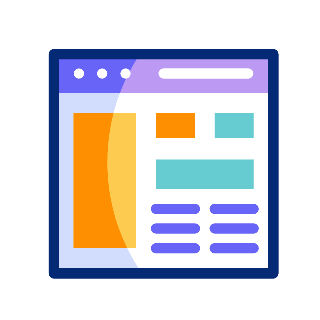
Use Multi-Location Monitoring
If you manage multiple warehouses, use Packem’s multi-location monitoring feature to track stock levels at each site. This will help you make more informed decisions about where to reorder stock.
DO YOU KNOW?
Frequently Asked Questions
Smart Reordering in Packem is a feature that predicts future inventory needs based on lead times, safety stock, and sales velocity. It automatically alerts you when it’s time to reorder from suppliers, ensuring you maintain optimal stock levels.
Reorder points are calculated based on factors such as lead time, safety stock, and sales velocity. Packem uses historical data and real-time sales trends to determine the best time to reorder products.
Yes, Packem allows you to monitor stock levels at multiple warehouse locations and helps you manage reordering for each site from a centralized platform.
Packem sends automatic email alerts to you and your clients when a product’s stock reaches its reorder point. This ensures that you never miss a critical reorder and helps prevent stockouts.
Yes, when stock reaches the reorder point, Packem can automatically generate purchase orders and send them to suppliers, making the reordering process fast and efficient.